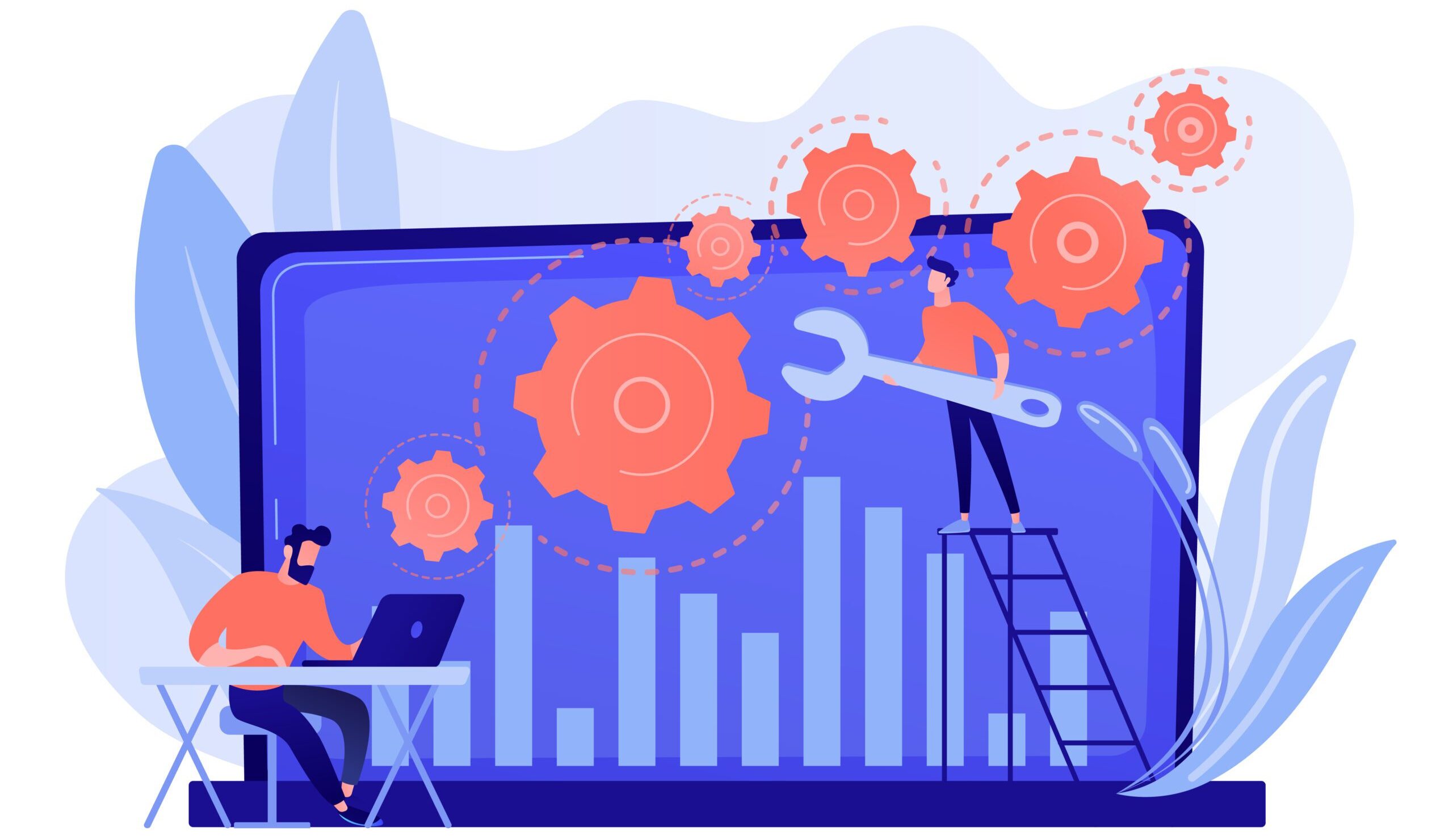
Streamlining Maintenance Operations starts with documenting of Maintenance activities and has been an integral part of any maintenance department. Be it a Continuous process plant, a discrete manufacturing plant, a batch manufacturing process, an Engineering type of industry, or any type of Industry. This will mostly start with a Logbook that is maintained on the Shop floor so that the Maintenance team(s) can enter the work being done on a shift-by-shift basis.
The History Cards are a further extension to this so-called documentation process and to include the breakdown history, PM’s preventive maintenance or any major refurbishing or reconditioning that may have been done on the machines or equipment.
Maintenance is inevitable as machines steadily wear down as you use them, hence the Maintenance function consists of a whole lot of discrete activities, that may or may not be under their control, and that’s where a lot of stress lies. So, you generate a lot of widespread data that needs to analysed and take action to ensure that Production isn’t affected because of machine failures.
Digitalization of Maintenance Data started way back when Excel Spreadsheets started being used regularly. But a spreadsheet isn’t a Database and multiple users using it simultaneously isn’t a good idea in the long run. Standardizing on the formats and reporting is a tedious task … and that’s how a #CMMS or a Computerized Maintenance Management System came into picture.
Please note that a CMMS is nothing short of an ERP for Maintenance. That’s why it is also referred to as an EAM or Enterprise asset management system.
What does a CMMS broadly have to have?
1. It should start with the standardizing of your information in a structured form, starting with a well-defined 4 to 5 level Plant structure & Asset Register,
2. Help maintain all the other master data that are properly validated and isn’t easily tampered with,
3. Integrating all operational activities in one place along with the Spares and manpower resources being used on them,
4. Helping in the planning of these resources as much as possible,
5. Providing Ready-to-use reports that help in monitoring KPI’s and smoothening operations,
6. Generating on-the-fly analysis to take fast action to ensure continuous improvements that get integrated in your daily operations,
7. An integrated TPM module or having an in-built Problem resolution process will definitely help in applying Best Practices,
8. A mobile enabled CMMS will certainly help in authentic data capture on the Shop floor,
9. Provide email and SMS Alerts and Notifications,
10. And last but not the least … it has to be fast-to-deploy and Simple-to-use!